放射線利用技術データベースのメインページへ
作成: 2005/10/10 日比野 豊
データ番号 :010288
イオン・プラズマを用いたマイクロ部材の表面改質技術
目的 :
プラズマ分解した炭素元素を、ミリからミクロンサイズの微細金型等にイオン化・堆積させたDLCにより、表面を耐食性、耐摩耗性、離型性等付与して高機能化する。
放射線の種別 :電子、軽イオン、重イオン
放射線源 :プラズマベースパルスイオン加速器(30keV、30A)
フルエンス(率):1015/cm2-1019/cm2
利用施設名 :全方位イオン注入装置(イオン工学センター製)、正負パルスイオン注入型成膜装置(プラズマイオンアシスト製)
照射条件 :炭化水素ガス 0.1-1.0Pa
応用分野 :マイクロ部品への耐摩耗性改質、離型性の改善、MEMS(マイクロ・エレクトロ・メカニカル・システム)部材の親水性、撥水性、生体親和性の向上、
概要 :
携帯電話や携帯端末などの液晶表示部やMEMS部材を成型する金型は、ミリからミクロンサイズの微細パターンが形成され、この表面の離型性、耐食性などの表面改質が望まれている。樹脂成形金型や成形品自身の機能性を高めるため、微細部分にアモロファスカーボン薄膜を、プラズマやイオン注入法を利用して、いかにして均一に表面処理するのか、機能を高める試みを紹介する。
詳細説明 :
近年、携帯電話やカーナビゲーター等の液晶パネルに用いられる導光板パターンは、高輝度・高精細化するため、数百ミクロンから数十ミクロンへの微細パターン化が進んでおり、ニッケル電鋳金型などが用いられる。しかしこの型を用いてアクリル樹脂やポリカーボネート樹脂を射出成型すると、成型時間と共に金型からの離型性が悪くなり、金型が変形・摩耗して使用できなくなる。
図1aは携帯電話用導光板パターンの微小突起物の一例を示し、1bはMEMS部品の微量血液による検査プレートの一例である。これら金型表面の離型性、耐食性、耐摩耗性向上のために表面改質が試みられている。
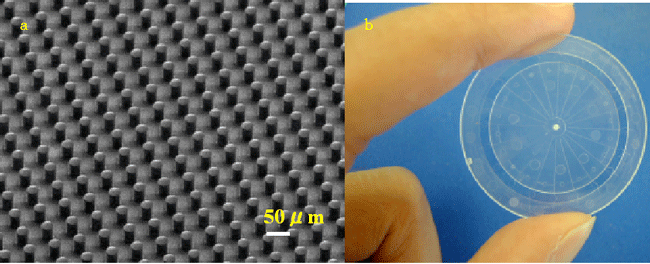
図1 マイクロ金型の一例(原論文1より引用)
表面改質被膜としてダイヤモンドライクカーボン(DLC)膜があり、この被膜をいかにして微細な穴や溝内部に密着性よく形成するのが大きな技術課題である。DLCは、炭化水素系ガスやグラファイトをプラズマ分解して、イオンビームのエネルギーを利用しながらSP3の構造とSP2の構造を併せ持ったアモルファスカーボン膜である。DLC中には水素が数%〜40%近く含有し、硬度や摩擦係数、耐摩耗性、電気的特性を大きく左右している。
DLC成膜法には、プラズマCVD法、イオンビームスパッタ成膜法、パルスイオン注入・成膜方法など採用されているが、そのH含有量は、原料ガス、プロセス条件、成膜手法によって異なり、現在多く利用されている摺動部品では、材質や形状ごとに最適な表面改質方法を選定している。しかしミクロンオーダーのパターンになるとイオン注入の指向性やプラズマ密度の関係から、微細内部への処理は困難を極める。
そこでプラズマやイオンビーム発生方法や処理物への電圧の印加方法の工夫により、いかにして微細な部分へ活性なラジカルを導くのか検討されている。
図2は並行平板型のプラズマCVD装置に置いて、メタン(CH4)、アセチレン(C2H2)、アルゴン(Ar)等のガス圧と、印加電圧によって生成されるDLCの硬度が、パイプ内面でどのように変化するか実験した結果の一例である。
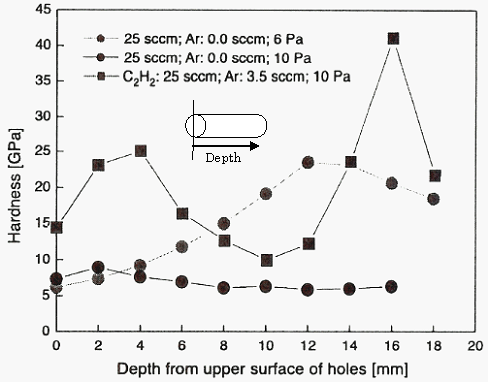
図2 プラズマCVDにおけるパイプ内面DLCの硬度変化 Copyright Elsevier (2004)(原論文2より引用)
サンプルとしてφ2ミリ、長さ20ミリのステンレス630パイプを用い、一端から所定の圧力でカスを流しながら高周波電圧を加えプラズマ化させ、サンプルに負電圧-8kVを印可してDLC成膜を1時間行った結果である。
アセチレンを6Paと10Pa及びアセチレン/アルゴン混合ガスを10Paで流し、パイプ内面長さ方向のDLC硬度分布を測定した結果、10Paでは長さ方向に硬度変化は少なく、7〜9GPaの柔らかいDLC成膜がされた。これに対して6Paで成膜したDLCは終端部分で25〜30GPaの高硬度なDLCが成膜された。
一方、10Paにおいてもアルゴンと混合して成膜した結果、入り口付近と終端付近で高硬度なDLCが得られ、中央部は10GPaと低かった。この原因はガス圧によってパイプ内でグロー放電が発生し、パイプ出入り口でプラズマ密度が変化する。プラズマ密度が高く反応速度が速すぎるとグラファイト成分の多いDLCしか得られない。プラズマ密度を下げてゆっくり反応させることが重要であると述べられている。
図3は印加する電圧を工夫して微細な溝内部にDLCを成膜する試みである。
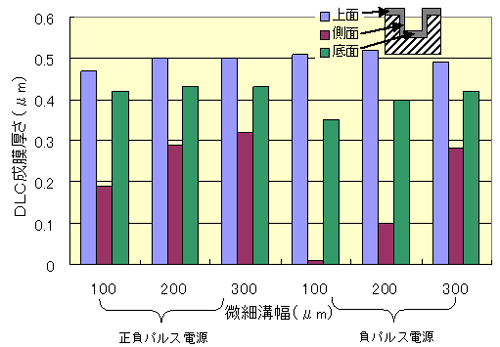
図3 正負イオン源による凹部内面DLCの成膜速度比較(原論文3より引用)
処理物に高周波電圧を印加してプラズマを生成させ、さらに処理物に負のパルス電圧のみ、あるいは正負のパルス電圧を印加して溝内部のDLC成膜速度を測定した結果である。サンプルとして100-300μm幅・深さのニッケル電鋳金型を用い、これに高周波電圧を印加してプラズマを生成させる。ここでμsオーダーの立ち上がりの正パルス電圧を印加してプラズマ中の電子を溝内部に照射する。この時の電子衝突により溝内部に高密度のプラズマが生成する。その直後に立ち上がりの早い負パルス電圧を印加することにより電子は追い出され、正のイオンを引き付けイオン注入される。
この正負の繰り返し操作を1秒間に1000回から4000回と高速で行うことにより微細部分までイオン注入が行われ、エネルギーを10kVから5kVへ低下させ、プラズマ重合反応によりアセチレン分解ガスを堆積させDLC成膜した。この結果、正電圧を印加せず負電圧のみで成膜を行うと溝上面はDLC成膜されるが、溝側面は大幅に成膜速度が遅く、100μm幅では殆ど成膜されなかった。これに対して正負電圧を印加することにより100μmの溝側面にも成膜されることがわかった。
以上のようにマイクロ部材の表面改質を行うにはプラズマ密度やバイアス電圧の印加方法が重要である報告されている。またマイクロ金型では離型性を付与する必要があり、メタンガス中にCF4等のガスを同時に導入してCF結合を形成して、DLCの硬度と滑り性を生かしながら離型性を付与する試みが行われている。その結果DLCに対する水の接触角は70度程度であるが、F導入により100度を越すと報告されている。
以上のように今後もマイクロ部材の表面の高機能化を目指して更なる研究開発が進められるものと思われる。
コメント :
光学用部品、電子機器部品の小型軽量化は今後さらに親展することは間違いがなく、それらに用いられる部材はミリからナノサイズへ移行していくと考えられる。それら部材の表面はバルク材料のままでは満足されず、表面改質の重要性が出てくる。近年の成膜プロセス開発によってその問題も解決され、より高機能を求めて研究開発が進められ、新規用途が期待される。
原論文1 Data source 1:
株式会社プラズマイオンアシスト社カタログ
日比野 豊
株式会社プラズマイオンアシスト
2005年版
原論文2 Data source 2:
Mechanical properties of DLC films prepared of micro-holes by pulse plasma CVD.
X.D.Yang, T.Saitp, Y.Nakamura, Y.Kondo, N.Ohtake
NGK INSULATORS,LTD,Nagoya,Japan
Diamond & Related Materials 13(2004)1984-1988
原論文3 Data source 3:
凹部品、パイプ内面へのDLC成膜
鈴木泰雄
株式会社プラズマイオンアシスト
イオン・プラズマフォーラム第17回3次元イオンプロセス研究会予稿集(京都2005-10)
参考資料1 Reference 1:
ゴム・プラスチック成形金型の離型性改善に関する研究開発
日比野 豊
株式会社イオン工学研究所
イオン工学ニュース,Vol 55(2003.12)
キーワード:プラズマ、イオンビーム、炭素材料、DLC、アモルファスカーボン、マイクロ部品、摩擦係数、耐摩耗性、機能性
plasma,ion beam, carbon material, diamond like carbon, amorphous carbon, micro part, friction coefficient, abrasion resistance, functional
分類コード:040101、040206、040306
放射線利用技術データベースのメインページへ